From Concept to Reality -The Nuances of Designing Electromechanical Machinery
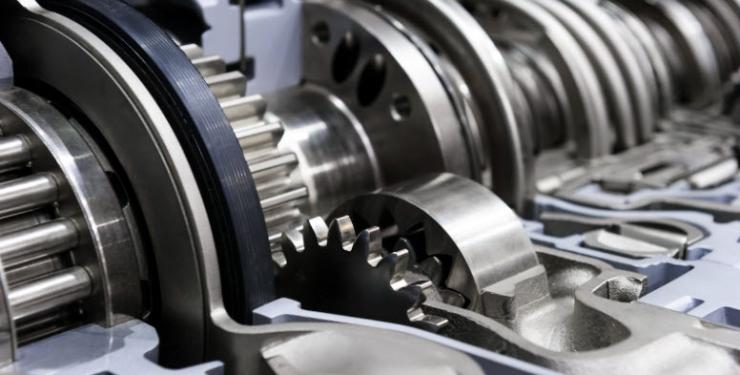
For every engine, generator, and or other electromechanical device, the path from initial concept to finished product is one that is long and arduous. And while considerable lead time is required to fulfill initial and subsequent orders, the design phase of product development is arguably much more intense and time consuming. In fact, it can take months and even years to determine all the relevant criteria that need to be addressed during the design phase. In this article, we’ll examine the factors and criteria that must be considered before an electromechanical device can transcend the design phase.
Establishing the Requisite Functionality of Mechanical Components
Communication and collaboration. These are the pillars of the early stages of the design phase. When it comes to designing electromechanical devices and systems, there must be frequent and open communication and collaboration between electrical and mechanical engineers. Not only is this key to understanding how each discipline will be utilized, but it also allows those involved to understand how their respective applications will work cohesively with one another. Consider for a moment, the humble motor. Each discipline must address their own respective challenges during the design phase. The mechanical engineer, for their part, may concern themselves with torque and inertia, and whether the motor can handle the acceleration and deceleration requirements. The electrical engineer, on the other hand, may concern themselves with power generation and distribution. Both must consider the environment in which the motor will be used. It is only by collaborating and integrating all design solutions will the motor be ready for use. Clearly, both mechanical and electrical engineers play different roles in the design of the motor, but the efficacy of function cannot be achieved without synergism between the two.
Generally speaking, the functionality of mechanical components of a system or device needs to be decided upon before the electrical requirements can be determined. Returning to the example of the motor introduced above, the electrical engineer would not be able to correctly size a servo motor if the mechanical engineer has not determined the mechanical requirements of the motor.
Key Factors to Consider
The subsections that follow are included to illustrate the most common design factors. Depending on the application, additional factors may need to be considered.
Cost
As one might expect, cost is one of the most important criteria that can directly impact the design phase of a product. In many ways, cost is viewed as a diametrically opposed factor relative to things like function and quality. It can also seem impossible to develop a product that ticks all the functionality boxes without inflating a budget or deflating a margin. In an age of intense competition, cost optimization must be baked into the design of a product, whether through process efficiencies or by establishing sound supply chain relationships.
Efficiency and Resource Management
Traditional manufacturing involved large machines that required an equally large power supply to operate. The current trend, however, has been for manufacturers to install energy efficient equipment that can produce quality products at high speeds. This often translates into leveraging automated or computer driven robotics to complete all manner of assembly tasks.
Strength
When designing an electromechanical device, it is expected that the individual components and the aggregate machine can withstand not only the conditions it creates during normal operations but also stand up to the environment in which it is intended to operate. As such, the design team must do their best to anticipate forces and other factors that could jeopardize the performance and shorten the expected lifespan of the machine.
Resistance to Wear and Tear
Wear occurs when two surfaces rub against one another causing the gradual removal of material. Over time, this material loss can compromise the strength and integrity of the component to the point of weakness or failure. During the design phase, surfaces that are prone to gradual wear should be identified and addressed accordingly. This can be achieved through process (i.e. regular lubrication as part of standard maintenance practices) or by sourcing harder materials that are resistant to wear.
Safety
There are many industry standards and legislation that govern the safety of products. The design phase of electromechanical equipment is vital to identifying and mitigating any potential dangers to the operator in adherence with well-established safety standards. Failure to consider and address a danger could result in serious injury and the component/device/machine being shelved or re-manufactured.
Ease of Assembly/Disassembly
Thanks to modern manufacturing capabilities, product design is no longer limited to the utilitarian. We have the capability of machining highly precise parts that lend themselves to relatively simple assembly and disassembly. If so designed, maintenance and repair activities are made much easier which in turn results in less downtime for the consumer.
Compatibility
Where possible, equipment should be designed in such a way that it can leverage the maximum number of standard components as possible. The benefits are three-fold. First, the use of standardized components will reduce the over cost of the machine. Second, it will be much easier to source spare parts. Lastly, it instills confidence in the end user that their machine can be more-easily serviced.
Ergonomics and Aesthetic Considerations
Of course, it is difficult to weigh any factor higher than functionality or safety when it comes to machine design, but aesthetics and ergonomics are also very important. After all, the device is difficult/cumbersome to use, causes discomfort, or lacks visual appeal, it could impact how it is used, even if it is otherwise highly functional. When designing a machine or other piece of equipment, due consideration should be given to these less obvious factors to enhance overall usability.
Creating Efficiencies in the Design Process
Finding strategies to optimize the design process isn’t always easy, but there are some tried and true methods that are used to facilitate the design of a system or machine.
Effective Concept Design Processes
It is important to leverage well established methods and tools that are ideal for flushing out a concept during the design phase. There are systematic methodologies that are particularly effective for electromechanical system design. On such methodology is the V-Model or Verification and Validation model which emphasizes the importance of testing and validation through each phase of the design process (e.g., Requirements Phase, System Design Phase, Subsystem Design Phase, Implementation Phase, etc.).
Multiphysics Simulation and Optimization
Advanced simulation tools that feature real world physics can lend significant aid to the design process. Notable examples include industrial Physics which allows expedited modelling and conversion of mechanical CAD data into physical models and 3Dexperience Simulation that specializes in predicting stress and deformation of industrial components, among other things. Utilizing these tools can add an incredible amount of efficiency to the design process.
The Path is Long, But the Results Speak for Themselves
The design of complex electromechanical equipment takes time, due in large part to the many factors that must be considered before production can begin. Though each component and application may differ in their challenges, the pursuit is worth the effort when we consider the many transformative machines that have benefited from careful and thoughtful design. Fortunately, there are many standards and tools that design teams can leverage to facilitate the design of these complex machines and systems. If you’d like to learn more about electromechanical systems, how they work, and how they are designed, consider enrolling in an engaging EM course at George Brown College.